Power Industry Solutions
Power Plant Coal Handling Measurement Solution
Accurate coal supply solution for power plants
This content is developed and original by Yike Electrical Technology Center, and has full intellectual property rights. It is only published on www.eaccor.com, Yike registered bidding platform and Yike belt weigher WeChat official account platform. Without the written authorization of Yike, please do not reprint/apply, and piracy must be investigated.
Current situation of coal management in Fossil fuel power station:
As the high consumption energy of Fossil fuel power station, coal directly determines the production and operation costs, energy consumption indicators, profit margins and overall business performance of the power plant. From incoming sampling, dumper, coal stacking, coal taking and coal blending, to furnace metering and coal feeder distribution metering, each link of the overall process needs to be linked, accurate and interdependent. In recent years, the fuel control efforts and requirements of various groups have been elevated to unprecedented new heights. The equipment department, power generation department, fuel department, and even plant leaders need to put a lot of effort into paying attention to and ensuring the safe, reliable, stable, and accurate operation of relevant equipment. Precise weighing and measurement and accurate calorific value analysis are required for coal entering the plant, which is the general gate for Fossil fuel power station to settle accounts. The use of precise weighing and measuring equipment mainly includes three aspects: 1) the actual operation of weighing and measuring accuracy; 2 is the stable period of accuracy within the allowable range; 3. Control the cost of manpower, material resources, and financial resources for later maintenance. This is the key pain point of Fossil fuel power station at present, and also the core problem to be solved, which directly affects cost control and business performance assessment. There are four main ways of transporting coal into thermal power plants: 1. shipping along the river and coastal areas; 2. Train transportation; 3. Automobile transportation; 4 is the conveyor belt at the pit mouth. All four methods require a review of incoming coal data, and a detailed analysis is as follows:
The first traditional shipping method is water gauge settlement, with significant errors coming from visual differences in the water gauge, changes in water temperature and density, ballast, and a deviation of 2% to 5%, which is normal. For current large ships transporting coal, it is a deviation of tens to hundreds of tons.
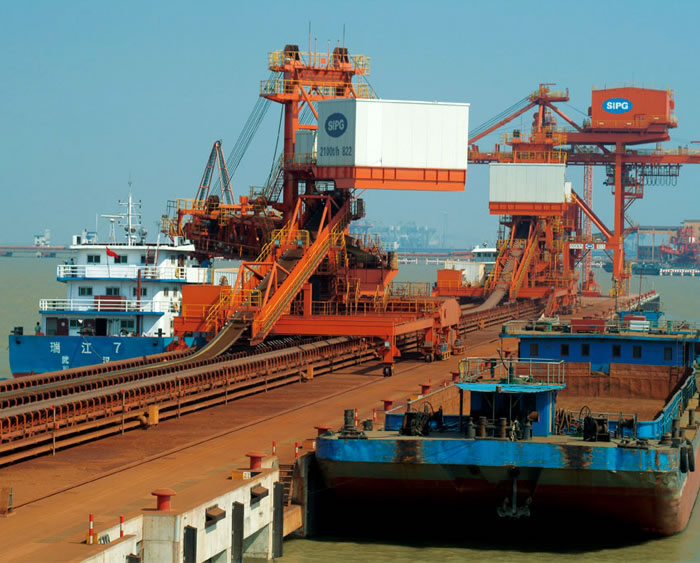
The second type of railway transportation fuel weighing measurement is relatively accurate, but the track scale has a series of difficulties and constraints such as large maintenance volume, high cost, and railway special operation, and it is difficult to detect equipment measurement errors in a timely manner< Br/>
The third mode of automobile transportation is relatively better, and there are now many unmanned weighing systems that prevent illegal operations such as cheating. The accuracy is relatively stable, and the main problem is that once the equipment has an out of tolerance problem, it is difficult for operation and maintenance personnel to detect it in a timely manner, which may cause significant economic disputes and losses< Br/>
The fourth type of pithead belt conveying method has high efficiency and low cost, and is settled by weighing and measuring the results using a belt scale. In the past, most pithead power plants were coal mine cooperative or self owned, with low requirements for specific coal quantity data, so using ordinary belt scales did not expose obvious problems. But with the increasingly strict requirements for modern enterprise management, the concept of industrial intelligence and refinement has deeply rooted in people's hearts. In order to improve its core competitiveness, enterprises must conduct detailed and accurate cost accounting, and even use industrial MES systems to conduct real-time online monitoring and assessment of various key links. The exposure problem of ordinary belt weighers is becoming increasingly serious, completely unable to meet practical work needs. Low weighing accuracy and unstable detection data can easily cause confusion in the accounts, often leading to shifting blame among departments, seriously affecting the quality and efficiency of daily business management work of enterprises< Br/>
If there is an intelligent belt scale that can achieve high-precision, self calibration, maintenance free, and high stability measurement for the four types of incoming coal measurement systems mentioned above, then the above problems will be easily solved. The patented technology product developed by Yike Electric in collaboration with foreign experts and university mentors after several years of innovative research and development& Flash; High precision fully intelligent matrix belt scale adopts advanced artificial intelligence weighing technology, equipped with specially designed ultra-high sensitivity sensors and artificial intelligence weighing controllers (using multiple sets of AD and more than 8 sets of weighing unit structures, the usage accuracy is maintained within 0.2% for a long time, the matrix arrangement, and the stability cycle of one calibration can reach more than 6 months, achieving worry free operation)! Equipped with a unique intelligent calibration system, each sensor has independent AD detection, fault alarm, and out of tolerance removal functions, ensuring that the belt scale maintains long-term high-precision and high stability operation. Self inspection and self calibration are unmanned, and the automatic calibration device is installed on the main scale body of the electronic belt scale. Its unique structure can simulate the gravity state of the transported materials in real time, and automatically complete the dynamic calibration management of the entire process of the belt scale. The secondary instrument adopts the SEQ-AI intelligent algorithm and matrix control tracking and review technology, and automatically completes monitoring, calibration and correction during operation and use. The first type of shipping can be changed to high-precision and fully intelligent belt scale settlement, which will be verified on-site by a third-party qualified institution and issued with certificates to ensure fair settlement without disputes. The second type of coal is transported by train, and the third type is transported by car. It can be compared in real-time through high-precision scales, which can timely determine extremely small out of tolerance data, prevent major trade disputes, and avoid losses. The fourth method is to transform the original traditional belt scale into a high-precision fully intelligent matrix belt scale, which can directly achieve accurate accounting,
Based on the diversity of the domestic fuel market, digital unmanned management and control of coal yard fuel is currently the trend. In order to effectively control costs from the source, major power generation groups are exploring innovative ideas and deeply tapping into potential to increase efficiency in digital management of coal yards and deep coal blending and burning of multiple coal types. The prerequisite for all control methods and advanced technologies to be put into production is the accuracy of coal stacking and coal extraction physical weighing and measurement. Whether stacking and reclaiming materials in open-air coal yards or fully enclosed coal yards, the traditional weighing method of bucket wheel conveyor belt scales can only achieve theoretical compensation for the upward and downward pitch angles, resulting in significant deviation in dynamic weighing measurement during stacking and reclaiming operations. The scale body is installed on the cantilever belt of the dynamic operating bucket wheel machine, and the accuracy is severely out of tolerance, the stability cycle is short, and it does not have automatic self inspection and calibration functions. Each calibration can only be manually carried out on the cantilever for manual code hanging. These factors have brought great difficulties to subsequent daily maintenance and calibration work. Even if a large amount of manpower and material resources are invested, the expected results cannot be achieved. The stacker and reclaimer operation of the bucket wheel machine plays a crucial role in the overall operation process of fuel from entering the factory to entering the furnace, as well as in transportation and transfer. The efficiency of the stacker process of the dump truck, the storage of materials in different zones according to coal types, and the coal blending and burning of materials in different zones, all require efficient, continuous, and stable operation of the bucket wheel machine. There is simply not much space and time for maintenance personnel to frequently maintain and verify the cantilever belt scale. However, the weighing and measurement data of fuel outbound and inbound is the core data that every power generation group inevitably monitors. The loss and profit of coal in the coal yard are of great importance. By inferring the weighing data of incoming coal from the weighing data of the track scale to provide a calculation method for outbound and inbound weighing and measurement data, the system error is too large and cannot be estimated at all, and it cannot reflect the actual working conditions in real time, directly, dynamically, efficiently, and accurately, Only extensive management can be carried out. In summary, in order to meet the requirements of refined dynamic whole process management of coal yards, the accuracy, stable cycle, real-time dynamic measurement, automatic verification, automatic verification, automatic monitoring, intelligent data identification and processing, daily maintenance, and other aspects of the bucket wheel conveyor belt scale are particularly important. They can be regarded as decisive factors affecting the overall management level of coal yards.
The "high-precision and fully intelligent bucket wheel conveyor belt scale" provided by IKE Electric can accurately weigh the bucket wheel crane during various dynamic changes in inclination and action posture, such as bidirectional movement, cantilever belt conveyor pitch, left and right rotation, etc. It is maintenance free during use, and the bidirectional independent measurement accuracy of stacking and retrieval can maintain weighing accuracy of ≤ 0.4% for a long time. Using more than 8 sets of matrix weighing units, equipped with dynamic attitude weight compensators, real-time, omnidirectional, high-precision tracking and detection of the three-dimensional attitude changes of the weighing unit during movement, real-time compensation and correction of the disturbance values of the symmetrical weight detection data, ensuring the stability and accuracy of the belt scale under various working conditions. The research on the technology of bucket wheel bidirectional stacking, reclaiming, weighing, and measuring belt scales has always been a challenge for the entire belt scale measurement industry, and it is also a shining pearl in the belt scale industry. Datang International Panshan Power Generation Co., Ltd. has solved the long-standing problem of coal yard accounting and management by using the high-precision and fully intelligent bucket wheel conveyor belt scale of Yike, and uploaded the weighing data in real-time to the "Three Major Fuel Projects" platform. Accurate material collection control is a key link in coal blending and combustion, and auxiliary coal yard metering and deep coal blending and combustion work are more high-quality and efficient.
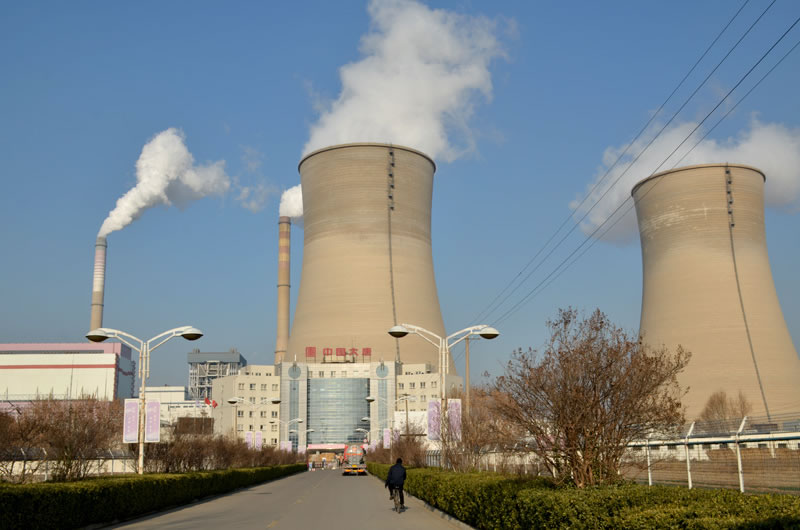
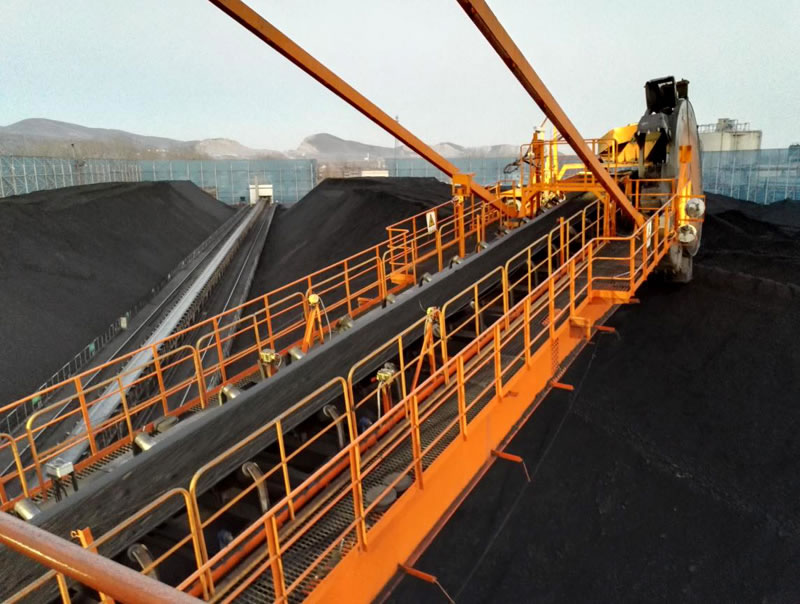
Datang International Panshan Power Generation Co., Ltd. No.1 Bucket Wheel
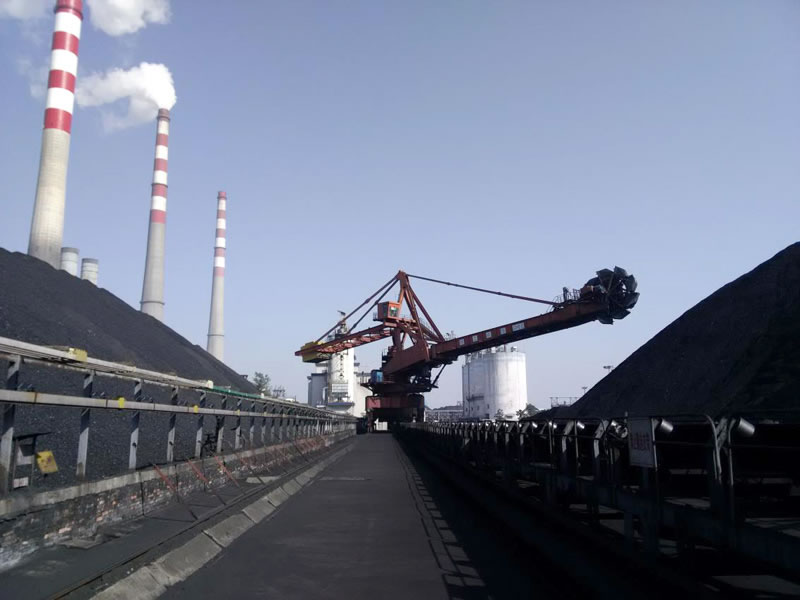
Huadian Xiangyang Power Generation Phase 2 No.1 Bucket Turbine
The measurement of incoming coal is the core data for calculating coal consumption in major power plants. There is a household appliance factory that installs two companies' Type 17 belt scales and circulating chain codes on each incoming coal belt, which is very helpless and inaccurate. There is no comparability between the two scales, and neither is accurate. Even the instruments purchased in the later stage are not guaranteed, with no factory name or model. It can be seen that traditional belt scales not only have fatal defects in themselves (see "Analysis of the Causes of Low Precision and Poor Stability of Traditional Electronic Belt Scales"), but also other chaotic phenomena. It is not allowed for anyone to do it, and if it is uncertain on site, the user will be blamed for the conveyor's failure, belt's failure, and roller's failure. If the cause cannot be found, it is the fault of on-site interference.
Yike Electric has issued a renovation plan for it, which has won the trust of users. We explain to them that you have suffered too much damage. Our high-precision fully intelligent matrix belt scale has an accuracy of ± 0.2% or more, a stability period of more than 3 months, self calibration, and maintenance free. If it fails to meet the usage requirements, we will provide users with a refund and return. Creating true value for users is the core business philosophy of Yike Company, and we always bear in mind the historical mission of "ensuring worry free operation and accurate measurement of all conveyors".
The high-precision fully intelligent matrix belt scale provided by Yike Electric for Datang International Panshan Power Generation Co., Ltd. uses physical hopper scales for verification and comparison, and the accuracy is always within 0.3%. When good, it can reach 0.117%, And the stability period has significantly increased (for the production management personnel of the power plant, 0.5% has already met the demand, and within 0.3% is an unexpected surprise. The long-term stability of accuracy within 0.5%, extremely low maintenance volume, and extremely convenient maintenance are several factors they are concerned about). The original imported Ramsey belt scale requires regular physical verification every 1 to 2 weeks to ensure weighing accuracy within 0.5%. The scale frame structure is equipped with two weighing sensors, and any problem with any component in the overall scale frame structure will directly cause the weighing measurement of the scale body to exceed the tolerance, directly affecting the stable operation of the conveyor. Moreover, due to its own structural characteristics, subsequent maintenance work is very inconvenient. The belt scale designed by Yike Electric is composed of 8 independent suspension weighing units, which are installed on 8 continuous rollers. The scale structure design, installation, and maintenance are extremely simple, and intelligent data processing and analysis instruments are equipped to automatically or manually remove out of tolerance weighing units. Individual weighing unit failures have minimal impact on the overall weighing data detection, ensuring the stable operation of the belt conveyor, It also provides sufficient time and space for maintenance personnel to work. After randomly removing one of the eight weighing units from the modified B-way belt scale, Pandian Company tested the weighing accuracy for one month, and the deviation was still controlled within 0.3%. This fully proves the fault-tolerant performance, stability, reliability, and accuracy of the high-precision fully intelligent matrix belt scale. If a belt scale malfunctions, the maintenance time can be independently selected based on the actual working conditions after the belt conveyor stops, completely avoiding the embarrassing situation of continuous overtime emergency repair of scale body faults, saving a lot of manpower, making the maintenance work more easy, efficient, and targeted. Yike Electric has effectively solved various pain points in the actual use of Ramsey's original imported belt scale, and takes on the responsibility of continuing to stand guard with a more accurate, stable, reliable, simple, intelligent, flexible, and convenient intelligent belt scale. Help users always stay at the forefront of fine management and efficiency in thermal power generation.
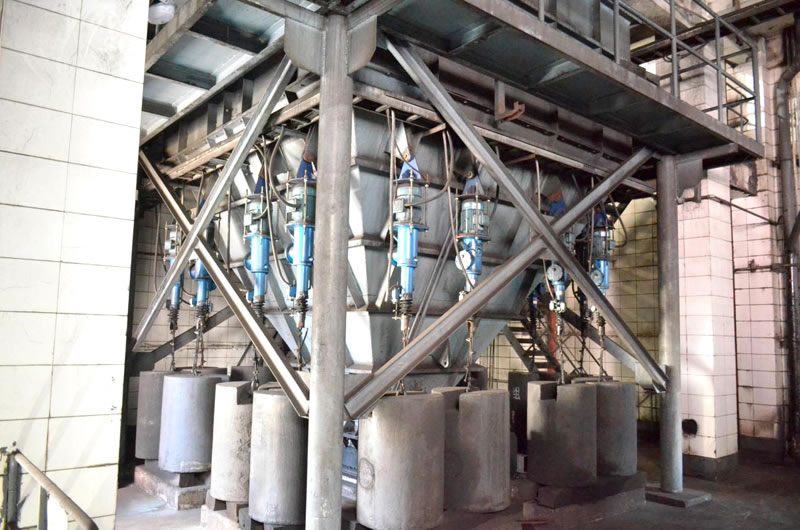
Datang Pan Electric Solid Material Bucket Scale
Datang Pandian High Precision Fully Intelligent Belt Scale
The importance of weighing and measuring the coal feeder belt scale:
In the automatic control mode, the control system automatically assigns the corresponding coal quantity command to the operating coal feeder based on the unit load command. The local control unit of the coal feeder performs closed-loop control of the belt speed through weighing data self detection to ensure timely response and effective control of fuel supply to unit load changes. In summary, the weighing and measurement of the coal feeder is fundamental and of utmost importance, and its accuracy and stability even directly affect the operation status of the unit.
The pain points of the coal feeder belt scale at present:
(1) At least three professional workers can cooperate with each other to complete the inspection, which is time-consuming and labor-intensive. Each calibration requires at least 2-3 people from the maintenance department to dismantle the heavy maintenance doors on both sides, the operating personnel to take relevant shutdown and isolation measures, and the thermal control personnel to perform zero and hanging code full calibration. The overall process takes at least 2-3 hours. Due to the cumbersome start-up and shutdown process of the on-site coal feeder, which is constrained by the comprehensive factors of unit load and actual working conditions, the maintenance and calibration conditions are very limited, resulting in very low work efficiency and inability to accurately estimate the time interval. This work has been deeply troubled by every cutting-edge professional in the thermal control and maintenance industry.
(2)Most coal feeder belt weighers use a Simple machine structure with two weighing sensors to lift the idler in the middle. Each calibration must first carry out the leveling detection of the overall frame, otherwise the calibration accuracy will be greatly affected. However, due to the small diameter and insufficient rigidity of the idler shaft project, coupled with the axial and radial displacement and vibration of the idler itself in actual operation, the weighing accuracy is out of tolerance and the detection data is unstable, Moreover, this weighing method cannot eliminate the impact of belt tension changes, and external factors such as belt deviation, roller sticking, and the interaction of internal stresses between two sensors are even more detrimental, making weighing accuracy, stability, and reliability impossible to discuss.
(3)The manual hanging of the code is very inconvenient. Due to the overall mechanical structure of the coal feeder, the hanging position is very narrow, with strong limitations, and the design is unreasonable. When hanging and retrieving the code, there is a risk of collision and injury to the maintenance personnel's arms, and the weight is easy to fall into the interior of the coal feeder. Some even require someone to extend their arm into the coal feeder and hang the weight at the connection between the corrugated pipe sensor and the thin shaft of the roller, and the weight can even scratch the belt.
(4) Without automatic verification and automatic verification functions, out of tolerance cannot be detected in a timely manner, and besides regular shutdown and code hanging verification, there are no other effective means with strong operability for detection and troubleshooting, making it impossible to effectively pre control critical nodes with deterioration trends. Unable to achieve status based maintenance and predictive maintenance.
(5) Due to the influence of the overall weighing framework design mechanism, the accuracy of weighing data is poor, the stability period is short, and the workload of later verification and maintenance is large< Br/> In summary, Yike Electric provides the following key technical solutions to help users effectively, conveniently, economically, and efficiently solve practical problems:
(1) Using precise matrix scale weighing technology to improve weighing accuracy to± 0.25%
(2) Replace the scale structure with a matrix dual scale weighing system, using high-precision pressure resistant advanced weighing sensors with temperature and linear compensation
(3) Select MW900Z matrix scale specialized instruments, high-precision weighing sensors, and digital speed sensors
(4) The calibration method has been changed to a specialized electric integrated calibration system for matrix scales
(5) Adjust the roller group and correction device to ensure the smooth operation of the coal feeder conveyor system
The high-precision, self calibration, and maintenance-free matrix belt scale provided by Yike for Datang Jixi Second Thermal Power Plant and Guodian Dawukou Thermal Power Company provides accurate and stable basic data for power plant calorific value calculation. It is also an important factor for accurate coal supply and coal saving
After years of on-site experience and careful exploration, IKE Electric is well aware of the pain points of users and equipment. We can provide users with more targeted, comprehensive, efficient, reliable, and economical solutions! Urgent for the user's needs, think about the user's thoughts!
Yike's mission: to ensure worry free operation and precise measurement of all conveyors
Yike's philosophy: creating true value for users
Reference documents:
1、《High precision and fully intelligent belt scale》
2、《High precision bucket wheel conveyor belt scale》
3、《High precision process scale》
4、《 High precision coal feeder》
5、《Analysis of the reasons for low accuracy and poor stability of traditional electronic belt scales》
6、《The core reasons and solutions for inaccurate weighing of traditional coal feeders》
7、《High precision pressure resistance matrix weighing coal feeder》
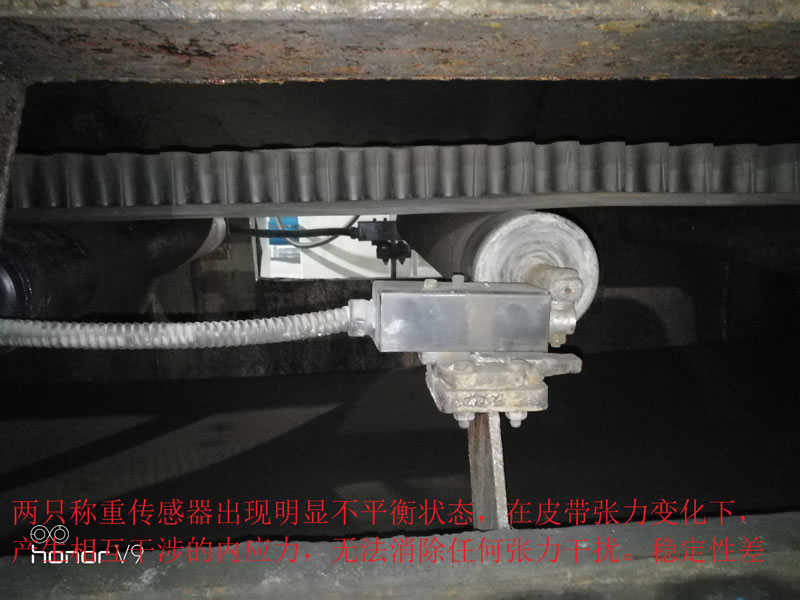
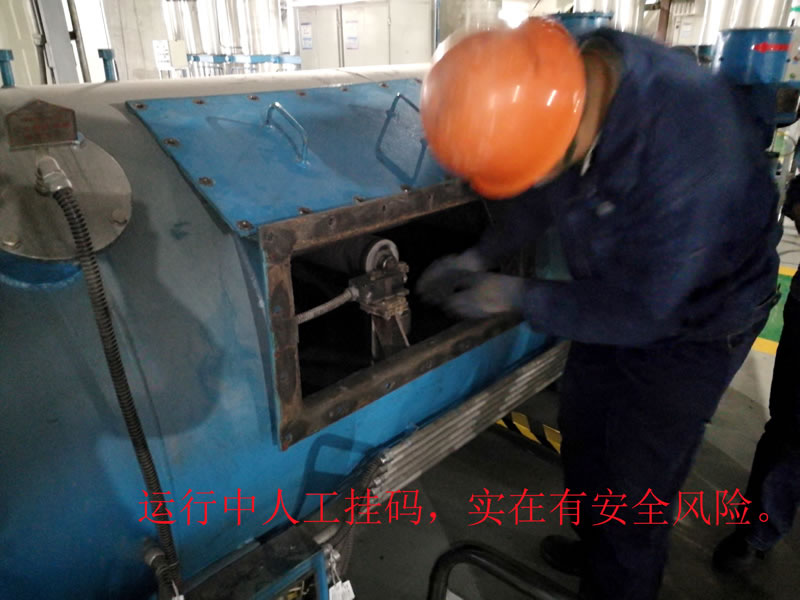
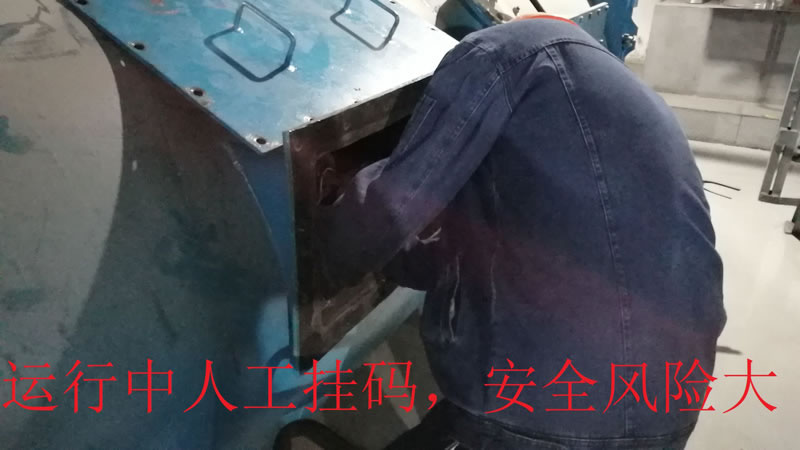
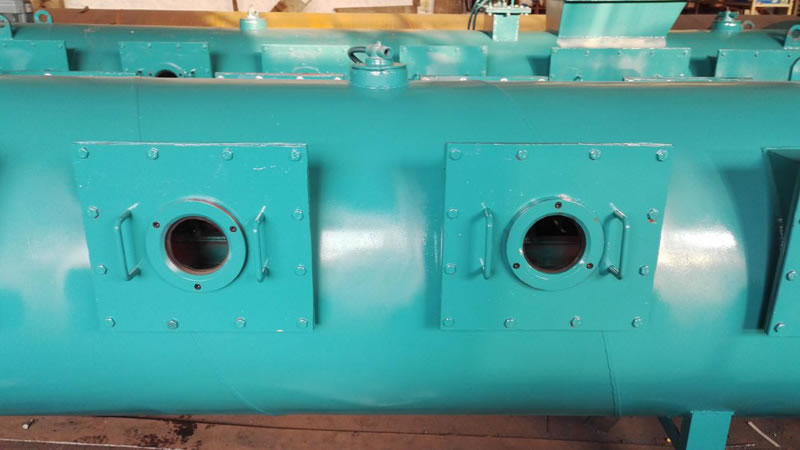
High precision matrix of Yike coal feeder
Reclaimer