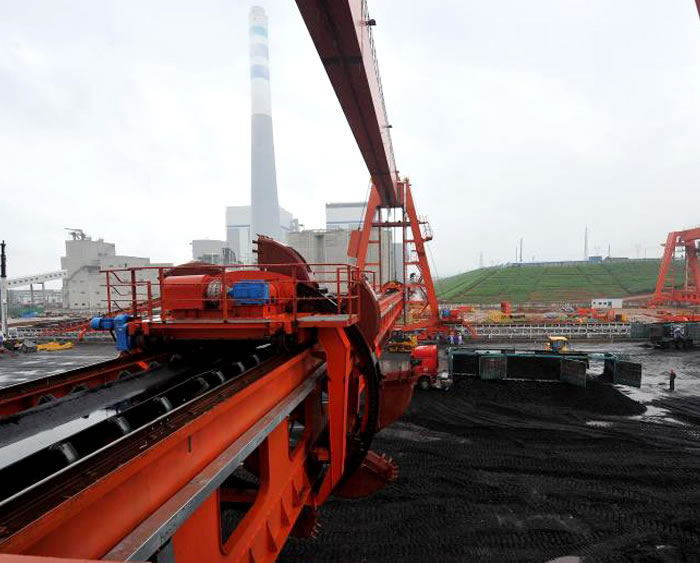
- Product name:High precision bucket wheel conveyor belt scale
- Product number:
- Usage accuracy:
- Product Overview:
Fully intelligent and high-precision bucket wheel conveyor belt scale
-------Dynamic weighing technology "Pearl on the Crown"
high-precision | check | maintenance-free |
Long term use and maintenance≤0.4% | 3-6 months | Worry free operation |
Yike Electric's "fully intelligent high-precision bucket wheel conveyor belt scale" can accurately weigh the bucket wheel stacker and reclaimer belt conveyor while it is moving, the rack is pitching, rotating left and right, and the inclination angle changes. It is maintenance free during use and can maintain weighing accuracy of ≤ 0.4% for a long time
system composition
The high-precision matrix scale mainly consists of four parts: n sets of B159A5 matrix weighing bridge, E897W imported speed sensor, imported MT8X digital converter, imported MW900X matrix scale specialized matrix intelligent instrument (with 8-16 separate AD sets), three-dimensional dynamic weight compensator ET1170, and temperature compensator PY50. The weighing sensors in the matrix bridge detect the weight of materials on the belt, and each group of matrix scales has a separate AD that is fed into a digital converter; The converter converts the analog quantity of the sensor into digital quantity and sends it to the integrator; The speed sensor directly measures the real-time speed of the conveyor belt, eliminating errors caused by monitoring the speed of the return belt or the speed of the active drum in the past, and sending the actual real speed information into the matrix intelligent instrument; The proprietary weight compensator ET1170, which places standard weight weights on an independent specialized matrix scale body, provides real-time actual weight signals when the angle of the bucket wheel crane arm changes and sends them to the intelligent instrument for weight compensation; The temperature compensator PY50 provides real-time environmental temperature signals to be sent to the instrument for temperature compensation of the entire system. The instrument processes the received speed and weight signals, and processes them through a proprietary matrix weighing and integrating intelligent data model to obtain the cumulative quantity and instantaneous flow rate of the material. The weighing sensor itself has special functions of temperature compensation and linear compensation, which improves the stability of the bucket wheel scale in case of leakage. Equipped with a weight compensator, designed specifically for stackers and reclaimers, it is far superior to angle compensators from other manufacturers and is an essential innovative tool for bucket wheel scales.
Core features of high-precision bidirectional metering matrix scale for bucket wheel stacker reclaimer
The variable angle matrix scale is a mobile belt scale developed on the basis of the matrix belt scale, which is installed on variable angle equipment such as stackers and reclaimers or mobile docks. The mobile belt scale adopts the "three-dimensional motion tracking compensation technology" and has a weighing accuracy of better than 0.2% in any inclination angle and direction from -18 ° to+18 °, and maintains a weighing accuracy of better than 0.4% in long-term use.
High precision attitude tracking system
High precision tracking and detection of three-dimensional posture changes in the weighing unit during movement, and compensation and correction of the impact of posture changes on weighing, ensuring accurate weighing of the belt scale in various motion states.
Sensor precise compensation technology
It can overcome the impact of temperature changes in the outdoor environment of the sensor and the impact of sensor zero point imbalance output. Independent temperature compensation is used to compensate for the environmental temperature variables of the entire conveyor, ensuring high accuracy even when temperatures cannot be reached.
Overcoming the influence of belt tension
The influence of belt tension is basically eliminated, and there is no requirement for symmetrical rollers, and there is no accumulation of empty belts.
Bidirectional calibration system
The operation of the conveyor in both stacking and reclaiming directions is essentially two different conveyors. The world of variable angle matrix scales has unique bidirectional calibration, fully integrating in two weighing environments in both stacking and retrieval directions, just like two scales running.
Low flow compensation system
Large flow fluctuation is the working feature of the bucket wheel stacker reclaimer at the ore terminal. Different ore densities vary greatly, and the bucket wheel itself changes in real time during the moving reclaiming process, which results in the actual situation that the flow of the same ore varies from high to low, and different ores work at different rated flows. In the production control of ore terminals, there is a practical need for stable and accurate measurement under various working conditions. To ensure accuracy in complex working conditions, especially during low flow operation, the variable angle matrix scale intelligent instrument implements low flow data verification and automatic compensation technology. In low flow operation, the sampling frequency of high-precision weighing sensors is increased and intelligent compensation is achieved, achieving high accuracy in low flow operation. The matrix scale itself is particularly suitable for measuring bulk materials with large fluctuations in flow rate.
Performance Comparison
Characteristics of Traditional Belt Scales |
Features of Siemens Belt Scale |
Advantages of Matrix Belt Scale |
Individual AD, non intelligent, single channel metering cumulative Total cumulative amount is 1 |
2/4AD, non intelligent, single channel metering cumulative Total cumulative amount is 1 |
4-16 AD, intelligent, dual metering cumulative, total cumulative of 2 |
Chinese display, regular black and white LCD |
English display, regular black and white LCD |
Chinese and English display, high-definition color screen |
made in China |
import brand |
import brand |
One set of four roller parallel bars |
1-3 sets of single roller scales |
Single/double idler self balancing Matrix unit 4-12 groups |
Unable to identify stacking and reclaiming materials |
Unable to identify stacking and reclaiming materials |
Automatic identification of stacking and reclaiming materials |
Can only be calibrated in one direction |
Can only be calibrated in one direction |
Bidirectional calibration, in both directions of stacking, operates like two scales. |
Return belt speed measurement Large speed error |
Motor speed measurement/rear drum speed measurement Large speed error |
Real time speed measurement of upper mounted belt weighing section No speed error |
No independent external temperature compensation |
No independent external temperature compensation |
Independent external temperature compensation |
The weighing sensor out of tolerance cannot self check and affect weighing. If one weighing sensor is damaged, it cannot measure and cannot automatically alarm. It is necessary to wait for manual discovery to cause production errors that cannot be detected. |
If the weighing sensor is out of tolerance and cannot self check, it will affect weighing. If one weighing sensor is damaged, it will not be able to measure and will automatically alarm. It must be replaced before measurement can continue. It affects production and must be shut down for maintenance. |
Weighing sensor out of tolerance self check, intelligent system automatically shields the out of tolerance scale and does not affect weighing. Damaged weighing sensors are automatically discarded and an alarm is given, even if two weighing sensors are damaged at the same time, it is not a problem. Other matrix scales continue to measure with high precision to ensure continuous production, and can be replaced when maintenance conditions are met. |
The analog angle compensator method has a large error and can only compensate for the upper and lower angles |
The analog angle compensator method has a large error and can only compensate for the upper and lower angles |
Configure a standard weight on a separate matrix scale to form a weight compensator, which can provide timely three-dimensional compensation as the boom angle changes up, down, left, right, and the bucket wheel moves |
Without this feature |
Without this feature |
High precision tracking and detection of three-dimensional posture changes in the weighing unit during movement, and compensation and correction of the impact of posture changes on weighing, ensuring accurate weighing of the belt scale in various motion states. |
Without this feature |
Without this feature |
The intelligent instrument system will process the data generated from each verification and use in the cloud, and self correct according to the characteristics of Data migration, so that each verification will be more accurate and the more accurate the data is, the more accurate the performance will be.
|
Verify stability once, with a period of 3-7 days |
Verify stability once, with a period of 3-7 days |
Verify stability once, with a period of 3-6 months |
The actual usage accuracy is not high, and the long-term stability is poor, making it difficult to maintain the accuracy during installation |
The actual usage accuracy is not high, and the long-term stability is poor, making it difficult to maintain the accuracy during installation |
Significantly improved weighing accuracy and good long-term stability |
Increase structural stiffness and bulky scale body |
The weight of a single roller is very light |
Significantly reduced stiffness requirements and weight reduction for symmetrical weight elements |
The structure of the belt conveyor needs to be improved to reduce belt tension changes, and the installation position must be selected at the location with the minimum tension |
The structure of the belt conveyor needs to be improved to reduce belt tension changes, and the installation position must be selected at the location with the minimum tension |
Effectively suppress the impact of belt tension changes, with wide requirements for installation position |
Structural deformation of equipment can lead to increased errors |
Single roller cannot overcome tension interference caused by roller deviation, shaft jumping, and uneven materials |
The impact of single support removal on structural deformation |
Not suitable for situations with uneven materials and large flow fluctuations |
ot suitable for situations with uneven materials and large flow fluctuations |
Especially suitable for situations with uneven materials and large flow fluctuations |
Weighing within the range of 40-100% |
Weighing within the range of .0-100% |
Weighing within the range of 5-100% |
Careful installation is required to ensure that the rollers are in the same plane |
Careful installation is required to ensure that the rollers are in the same plane |
Reduced requirement for coplanarity of symmetrical heavy rollers |
Careful maintenance is required to prevent the rollers from getting stuck with materials |
Careful maintenance is required to prevent the rollers from getting stuck with materials |
Minimal maintenance, no impact on roller sticking |
Trade settlement disputes are significant and rarely used for trade measurement |
Trade settlement disputes are significant and rarely used for trade measurement |
Suitable for trade settlement and important bulk material measurement |
Ordinary scales for bucket wheel machines |
Ordinary scales for bucket wheel machines |
High precision matrix scale specifically designed for bidirectional measurement of bucket wheel machines |
Application scope
◆ Weighing of bucket wheel stacker reclaimer belt conveyor
Installed on the cantilever of the stacker reclaimer, in situations where the inclination angle of the belt conveyor is variable. Accurate weighing can be carried out while the entire belt conveyor is moving, the rack is pitching, rotating left and right, and the inclination angle changes. It is maintenance free during use and can maintain weighing accuracy error of ≤ 0.4% for a long time
◆ Fabric control
The high-precision stacking and reclaiming belt scale, combined with GPS three-dimensional scanning technology, obtains the stacking rows and material layer distribution in the material yard, accurately controls the thickness of the material layer in the material yard, and vigorously improves the quality of mixed materials.
◆ Mobile belt weighing
Suitable for weighing belts with varying inclination angles as the water level changes when the tail of the belt conveyor is installed in a dock moving dock; Belt conveyor is installed on mobile devices, and various belt weighing occasions where the installation status of the belt conveyor changes during weighing.
Yike Electric: 400-688-2588
Prev:Intelligent control array electronic belt scale
Next:High precision electronic belt scale