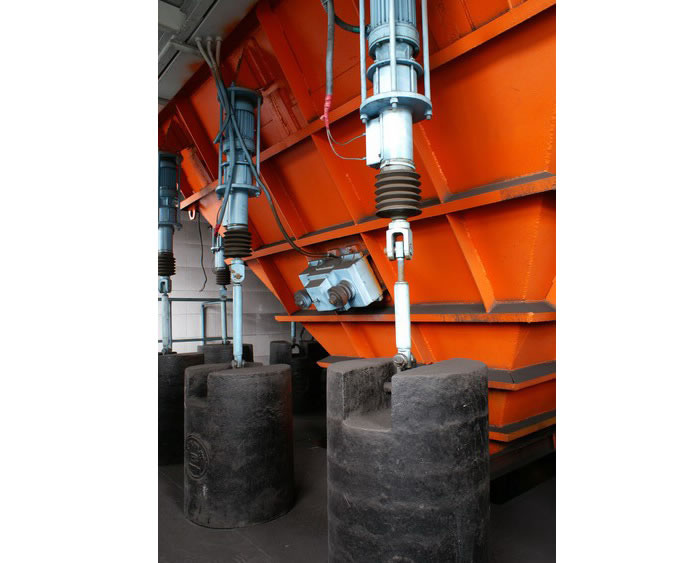
- Product name:B168 Belt Scale Physical Verification Device
- Product number:EMCB1608002
- Usage accuracy:
- Product Overview:
24-hour service: 400-688-2588
EACCOR-B168 Belt Scale Physical Verification Device
Product Description: The EACCOR-B168 electronic belt scale physical verification device is a high-precision static electronic scale designed specifically for online calibration and verification of belt scales. The physical inspection system has made the previously complex, time-consuming, and labor-intensive physical inspection and calibration of belt scales simple, fast, and reliable.
The EACCOR-B160 electronic belt scale physical verification device is a high-precision static electronic scale designed specifically for online calibration and verification of belt scales. The physical inspection system has made the previously complex, time-consuming, and labor-intensive physical inspection and calibration of belt scales simple, fast, and reliable.
The volume of the hopper in the electronic belt scale physical verification device system depends on the conveying capacity of the conveyor where the belt scale is installed. According to the regulations of the original Ministry of Electric Power [1993] No. 457 document, when using real coal for verification, the amount of coal inspected shall not be less than 2% of the maximum hourly accumulated quantity during the operation of the coal conveyor belt.
In order to ensure the accuracy of the physical calibration device for electronic belt scales, the calibration device itself should be equipped with self checking weights (i.e. standard devices) for easy calibration at any time. The weight configuration is in accordance with the JJG (Electric Power) 02-96 verification regulation of the Ministry of Electric Power: the minimum weight value of the standard weight used for verification is 1t, or 50% of the maximum weight, whichever is greater, and the rest can be replaced by any other constant load. The accuracy of the standard weight is M11 level.
This device can not only be used as a calibration device for belt scales, but also as a measuring device for bulk materials such as coal, ore, grain, cement, etc.
Working principle:
The working principle of the physical inspection device is that when the material on the belt conveyor is weighed by an electronic belt scale and enters the weighing hopper, the four weighing sensors supporting the weighing silo will generate an electrical signal output proportional to the weight value of the material. The output signal enters the microprocessor controlled weighing display instrument, which amplifies and processes the signal to display the actual weight. After weighing, the material is returned to the conveying system through the discharge equipment. Compare the material weight displayed by the physical detection device with the belt scale to achieve the purpose of verifying the belt scale. The above weighing method involves first passing the material through a belt scale and then weighing it through a hopper scale. Materials can also be pre weighed through a hopper scale and then weighed through a belt scale. Which method to use will be determined based on the on-site situation.
In order to ensure the accuracy of the physical inspection device, it is equipped with standard weights for the approval of its own accuracy. Usually, before testing, a weight lifting machine is installed on the weighing silo to lift the standard weight, and the weighing instrument will display the weight of the lifted weight. The displayed value should be the same as the weight value, otherwise, the symmetrical weight display instrument will be corrected. The weight lifting machine is programmatically controlled through a programmable controller for lifting and lowering, and can also be manually controlled through the operating platform.
In order to improve the automation level of the system, a computer can be selected for bidirectional communication between weighing instruments, belt scale instruments, and programmable controllers to manage them and make their weighing and calibration automatic. By using the AUTO-MAT (automatic material calibration) software specifically designed for Qijie, the interval value of the belt scale can be automatically corrected, so that the displayed value of the belt scale instrument is the same as the displayed value of the weighing display instrument, in order to avoid human operation errors. On the computer screen, the weighing of hopper scale, belt scale and weight lifting can be completed, and the above working process can be Dynamic simulation.
In addition, during normal operation of the belt scale, the industrial control computer can monitor the operating status of the belt scale in real time, record the curves of the transported materials, and print various related reports. The printing format can be completed according to requirements, including shift reports, daily reports, briefings, quarterly reports, and annual reports.
Work process:
There are two main ways for the system to work:
1、 After the actual material enters the silo through the feeding port, the weighing display instrument outputs the weight display. Record the displayed weight as the reference weight for verifying the belt scale. Open the discharge door, and this standard material will flow to the lower conveyor belt installed with an electronic belt scale for calibrating the electronic belt scale.
2、 The material passes through the conveyor belt equipped with an electronic belt scale. It is first weighed by the electronic belt scale, and then the actual material is fed into the silo through the feeding port. The weighing display instrument outputs the weight display, records the displayed weight as the reference weight for verifying the belt scale, and opens the discharge door. This material will flow to the lower conveyor belt.
System features:
·System comprehensive accuracy: 0.05%
·The weighing silo can be improved on the existing buffer silo, or a new design can be carried out
·The weighing sensor is installed in a bridge structure without the need for limit positioning
·Digital instrument with high accuracy and good stability
·Quick keys can be used to operate automatic zero and interval adjustment
·The electrical control part adopts a programmable controller, which allows users to expand their functions
Hopper system
The weighing hopper body is made of high-quality steel plates. Strengthening measures shall be taken at stress concentration points, and external reinforcement shall be used as reinforcing bars. The joints around the weighing bucket are smooth, and the angle between the four walls of the weighing bucket and the horizontal line meets the requirements. The intersection of the two walls is in a circular arc transition. The upper and lower openings of the weighing hopper are well sealed. Install a vibrator on the weighing hopper and vibrate it in a timely manner after unloading to avoid material accumulation. To ensure safe and convenient transportation, the scale body and frame are of a combined type, and they are pre assembled in the factory and welded on site.
Weighing control system
Load Cell
Rated output: 1.5mv/v ± 0.1%
Non linearity: 0.02%
Repeatability: 0.02%
Creep: 0.03%
Excitation voltage: 10-15VAC/DC
Input resistance: 650 Ω ± 5 Ω
Output resistance: 605 Ω ± 5 Ω
Temperature range: -20 ℃~+60 ℃
Safety overload: 150%
Ultimate overload: 200%
Protection level: IP67
eaccor-9000 Static Weight Indicator
The 9000 field mounted and panel mounted integrators are controlled by microprocessors to process the weight signal of the weighing sensor, calculate the weight value, and display it on the instrument. An additional communication board can be used to communicate with the upper computer using RS-232 or RS-485 interfaces.
The instrument adopts a fully Chinese operation interface, which is intuitive and easy to operate. And it has multiple automatic detection functions, making it easy for users to calibrate and maintain.
Note
Environmental parameters
1. The indoor/outdoor installation location should be as close as possible to the weighing sensor, and attention should be paid to dust and moisture prevention.
2. Storage temperature -40 ℃ -+70 ℃; Operating temperature -10 ℃ -+40 ℃
3. Maximum relative humidity: 95%
source
·220VAC ± 10% 50Hz
·Fuse 2A
·EMI/RFI filter
Load Cell
·The instrument provides a 10VDC ± 10%, 200mA excitation power supply, and can be connected in parallel with four weighing sensors
·Sensitivity, 0.7mV/V – 3.5mV/V
·Maximum input signal 33mV
·Weighing sensor shielding grounding
·When the cable distance is greater than 60 meters (not exceeding 900 meters), an excitation compensation circuit is used
·Local or remote compensation selection
Note
electric control system
The calibration process adopts PLC control method. The equipment can be operated manually or by an industrial computer on site, and self calibration and display and statistics of belt weighing timing data can be achieved by reading the signal of the weighing instrument. There are sufficient communication interfaces between the physical calibration device and the coal conveying system.
self check
Weight lifting machine
The electric weight lifting machine is reliable, stable, and has a simple and reasonable system, which can ensure the novelty and correctness of sensor force. This device is in a relatively advanced position in China.
B standard weight
Weight: 1000kg or 2000kg each.
Standard weight accuracy level: M11 level
Prev:EACCOR-B166 Automatic Cyclic Chain Code Verification Device
Next:PJ type physical calibration device